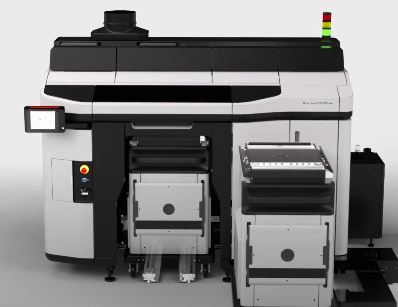
Industrial 3D printers have ushered in a new era for manufacturing, transforming how companies approach production and prototyping. These high-tech machines are redefining traditional processes, offering faster, more cost-effective, and innovative solutions. Whether it’s producing parts for aerospace, automotive, or consumer goods, industrial 3D printers are providing businesses with unparalleled flexibility, speed, and efficiency.
What Are Industrial 3D Printers?
Industrial 3D printers are large-scale machines that utilize additive manufacturing (AM) to create parts layer by layer from digital models. Unlike traditional subtractive manufacturing methods, such as milling and turning, which remove material to shape a part, 3D printing builds up material to create complex geometries. This additive process enables the production of highly intricate and customized designs that would be difficult or impossible to achieve with conventional techniques.
These printers can use a wide variety of materials, including plastics, metals, ceramics, and composites. Depending on the technology used (like FDM, SLA, or SLM), the properties of the final product can vary, providing versatility for different industrial needs.
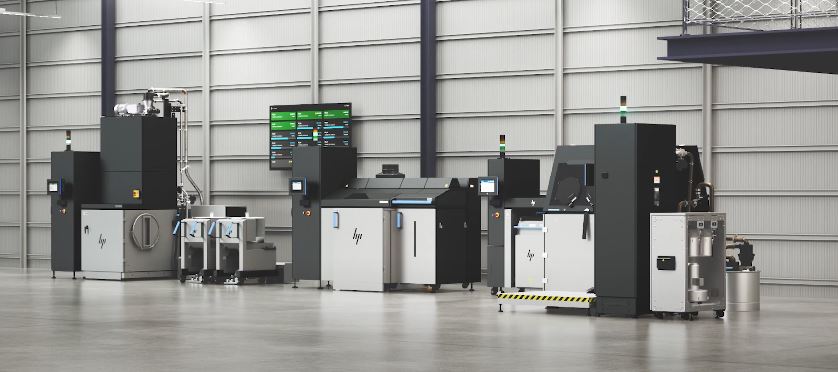
Benefits of Industrial 3D Printers for Production
Faster Prototyping
In the past, creating prototypes required costly molds and tooling, which could take weeks or even months. With 3D printing, prototypes can be produced in hours, allowing for rapid iteration and testing. Designers and engineers can evaluate physical models in real-time, making improvements and adjustments much faster.
Cost Efficiency
Traditional manufacturing methods often require expensive tooling, molds, and material waste. 3D printing reduces the need for these investments. The process is highly efficient, as material is used only where necessary, significantly lowering costs, especially for low-volume production.
Complex Geometries
Industrial 3D printers can produce highly complex and intricate shapes that would be impossible or very expensive to create with traditional methods. This capability opens up new possibilities in design, such as lightweight structures for the aerospace industry or highly customized parts for consumer products.
Customization
3D printing allows for high levels of customization, whether it’s for a one-off part or a limited run of bespoke products. This flexibility makes it ideal for industries like healthcare, where customized implants, prosthetics, or medical devices are in high demand.
Reduced Material Waste
Traditional manufacturing methods often involve material waste, especially when machining parts from blocks of material. 3D printing, on the other hand, uses only the necessary material, reducing waste and contributing to more sustainable manufacturing practices.
Future of Industrial 3D Printing
As 3D printing technology continues to evolve, the potential applications in industrial production are endless. With advancements in material science, we can expect to see more diverse materials being used for production, including biocompatible materials for medical implants or stronger, more durable composites for automotive parts.
Additionally, the integration of artificial intelligence and machine learning into 3D printing systems is poised to enhance their capabilities, allowing for even more efficient production and smarter design optimization. As costs decrease and technologies become more accessible, more industries are expected to adopt 3D printing for a wider range of applications.